Our Products
Polyacrylamide / High Molecular Weight Anionic polyacrylamide emulsion used for Friction Reducer
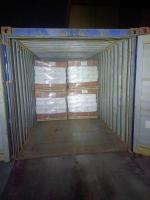
Application of Anionic Polyacrylamide Emulsion as a Friction Reducer
1. Introduction
Anionic polyacrylamide (APAM) is a water-soluble polymer known for its exceptional flocculation properties, high molecular weight, and versatile functionality. One of the most impactful applications of APAM, particularly in its emulsion form, is its use as a friction reducer in various industrial processes. The most prominent industry utilizing APAM-based friction reducers is the oil and gas sector, specifically in hydraulic fracturing operations, although its use extends to pipeline transport, mining, municipal water treatment, and pulp and paper industries.
This document discusses the structure, mechanism, and detailed applications of APAM emulsion as a friction reducer, emphasizing its advantages, preparation, environmental implications, and technological advancements.
2. Chemical Structure and Properties
Anionic polyacrylamide is a linear, high molecular weight polymer derived from acrylamide and acrylic acid or its salts. The anionic nature comes from the carboxylate (-COO⁻) groups introduced during copolymerization. In emulsion form, APAM is suspended in a water-in-oil matrix with surfactants that help maintain its stability.
Key properties relevant to its role as a friction reducer include:
-
High molecular weight (typically 10–20 million Da)
-
Strong hydrophilicity
-
Shear-thinning behavior
-
Rapid hydration and activation (especially in emulsion form)
-
Excellent solubility in water once activated
These features make APAM especially suited for applications where it must act quickly under high-shear or turbulent flow conditions.
3. Mechanism of Friction Reduction
In fluid transport systems, especially pipelines and hydraulic fracturing, fluids experience resistance from contact with pipe walls, internal turbulence, and particle collisions. This resistance, or friction, requires more energy to move the fluid, increasing operational costs and decreasing efficiency.
When APAM is added to water-based fluids in small concentrations (typically 0.05–0.5%), it aligns itself along the flow direction, forming extended polymer chains. These chains suppress turbulence and reduce the energy dissipation caused by eddies and chaotic flow. This is known as the Toms effect, named after B.A. Toms who discovered the phenomenon in the 1940s.
As a result, drag reduction of up to 70% can be achieved, leading to significant cost savings in pumping operations and enabling higher flow rates with the same energy input.
4. Applications in Hydraulic Fracturing
Hydraulic fracturing is a key method for extracting oil and gas from low-permeability shale formations. It involves injecting high-pressure fluid into rock layers to create fractures, allowing hydrocarbons to flow more freely. The fluid, commonly called frack fluid, consists of water, proppants (such as sand), and various chemical additives—including friction reducers.
Role of APAM Emulsion in Fracking:
-
Friction Reduction: Reduces pumping pressure requirements, allowing higher fluid volumes to be injected into the wellbore with lower horsepower.
-
Water Solubility: Rapid dissolution ensures minimal mixing time on-site, a critical aspect in continuous fracking operations.
-
Emulsion Stability: The emulsion form allows for better handling and storage in field conditions, offering longer shelf life and ease of metering.
-
Compatibility with Other Additives: APAM emulsions are generally compatible with biocides, scale inhibitors, and surfactants commonly used in fracking fluids.
-
Minimized Equipment Wear: By reducing pump strain, APAM prolongs the lifespan of high-pressure equipment.
In unconventional shale reservoirs, where large volumes of water are pumped at high rates (often 80–100 barrels per minute), the use of an effective friction reducer like APAM is essential to maintain operational efficiency.
5. Applications in Pipelines
Friction reducers are also critical in long-distance transport of fluids through pipelines, whether for crude oil, slurry, or wastewater. In such systems, APAM emulsions are used to:
-
Reduce drag in turbulent flow conditions.
-
Increase throughput by allowing higher flow rates without expanding infrastructure.
-
Reduce energy consumption by decreasing the required pump pressure.
-
Improve efficiency in slurry pipelines by stabilizing particle suspension and flow.
The ability of APAM to function effectively at low concentrations makes it economically attractive for pipeline operations, where even minor efficiency gains can result in significant cost reductions over time.
6. Use in Other Industries
Although most prominently used in oil and gas, APAM-based friction reducers are also applied in:
-
Mining: Slurry transport, tailings disposal, and water recycling.
-
Municipal Water Systems: Reducing energy requirements in large-scale water distribution networks.
-
Pulp and Paper: Enhancing flow in paper machine white water systems.
7. Preparation and Handling of APAM Emulsions
APAM emulsions are supplied in a stable, concentrated form but require proper dilution and activation before use. Key considerations include:
-
Dilution Systems: Inline or batch mixing systems are used to activate the polymer before injection.
-
Hydration Time: Emulsions hydrate more rapidly than dry powder forms, typically within 3–10 minutes.
-
Temperature and pH Sensitivity: APAM is generally stable in neutral to slightly alkaline conditions but may hydrolyze under extreme pH or temperature.
Handling guidelines emphasize the importance of avoiding shear degradation and ensuring proper mixing to avoid "fisheyes" (undissolved polymer clumps).